
From rising demand for new school places to the deteriorating state of primary and secondary schools across the country, the UK education sector is at a crossroads.
The Government’s Build Back Better strategy, which includes a £14 billion investment in schools to help with expansion and renovation projects, is a welcome step in the right direction. But if we are to meet our targets quickly and sustainably then we need to start looking at more efficient ways to build our schools.
‘Offsite’, a word used to describe the manufacture of building components in a factory setting that are then brought to site and assembled for construction is one way we can achieve this, but this potential is amplified when twinned with a strong system of collaboration. One example of this was the recently completed expansion at Addington School, an OFSTED-rated Outstanding Special School for children and young people with special education needs and disabilities.

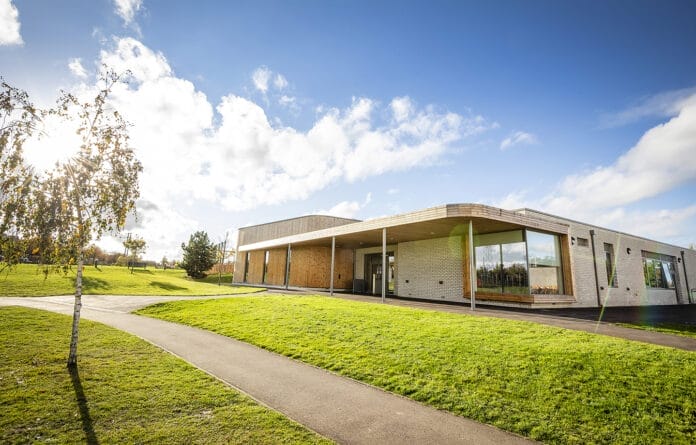
HLM Architects teamed up with Reds10 and Wokingham Borough Council to create a new standalone 50-place facility which involved over 70 per cent of the building being manufactured offsite.
Design engagement took place at the very onset and ran over a period of eight weeks. BIM Level 2 and data-led technology enabled the team to work closely together, efficiently and creatively, putting user needs at the forefront and adjusting designs when necessary early on. This meant time was used efficiently at the front end of the process, which enabled manufacturing to begin much more quickly.

The fact that so much of the work took place in the factory minimised disruption to the school, its pupils and surrounding community, as well as significantly reducing the overall programme for delivery.
It also meant there was more scope for early engagement with the school team in the design decision making process. Involving them at this formative stage helped to establish a holistic digital and offsite strategy, unlike the traditional approach where this can often get missed.
Regular workshops and digital collaborative tools also kept the entire stakeholder team – including the school, local authority, and design and supply chain teams – in close contact throughout. Site visits as well as visits to the factory kept everyone involved informed throughout the manufacturing process and allowed them to review progress. This interaction also helped the school and its pupils celebrate key milestones, including the delivery of assembly modules.
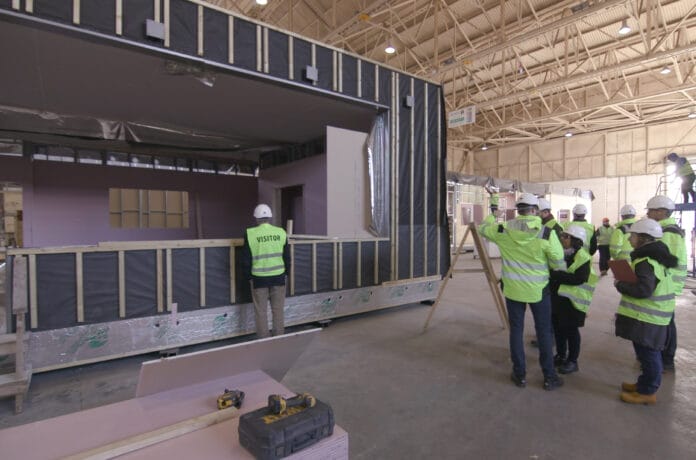
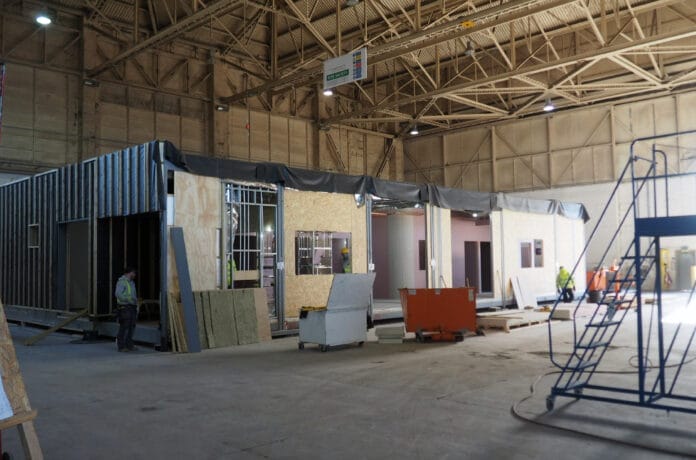
In conjunction with HLM Architect’s ‘Think: Off-site First’ initiative – a commitment to delivering projects primarily using the off-site manufacture approach – conceptual designs were based on a deep understanding of the school and the student’s complex needs. The modular system allows for flexibility in frame sizes, and are not confined to one size, which gives added flexibility when designing the layouts.
The team then created a library of building components, some of which are assemblies of multiple components, to make standard building elements such as rooms, walls, hygiene rooms, door sets and ceiling types etc. They were able to create a ‘kit of parts’ that reflected preferred approaches to construction that were affordable and reliable.
These kits resulted in a very efficient and robust approach to design and construction, enabling the team to achieve large span spaces and apertures to allow greater natural light. To create a unique identity for the school, HLM Architects worked closely with the steelwork fabricator to achieve non-standard offsite architectural features such as a curved double-heighted wall, requiring faultless precision. An external canopy at the front of the building, which wraps around the façade, also pushed the boundaries of what can be achieved in offsite design – the result of close coordination between HLM Architects, Reds10, structural engineer, and the fabricator.
Manufacturing offsite meant that embodied carbon through the construction process was minimised. The building also features operational carbon reduction features such as natural ventilation units and air-source heat pumps. Any timber used in the construction of the building was responsibly sourced and Forest Stewardship Council (FSC)-certified.
Bespoke sensory spaces were designed to nurture a therapeutic environment for children. The spaces are monitoring and evaluation-driven and equipped with mechanical hoists and adjustable components. The extension and additional social spaces also feature a sensory path and specialist play area sitting proudly within the existing school landscape, enhancing the user experience for years to come.
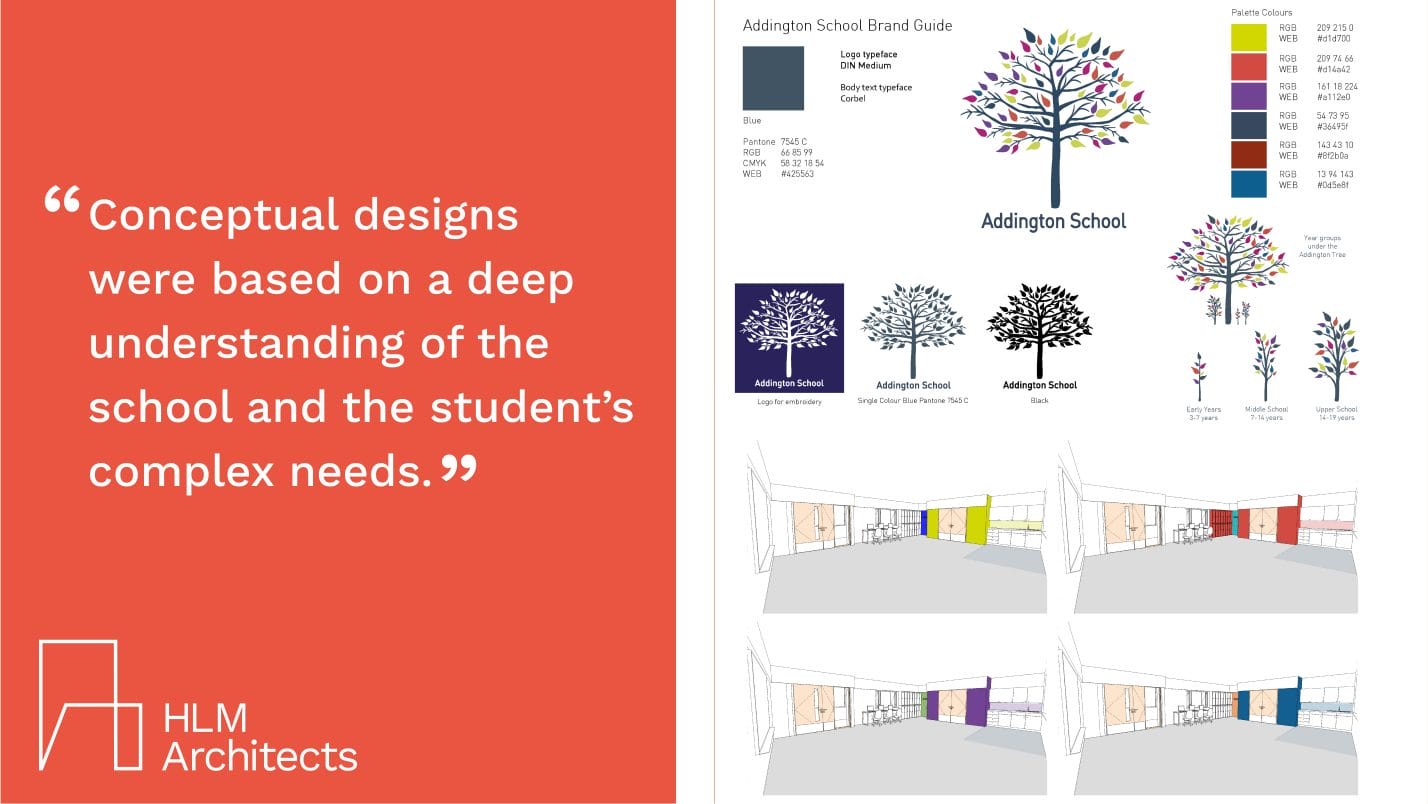

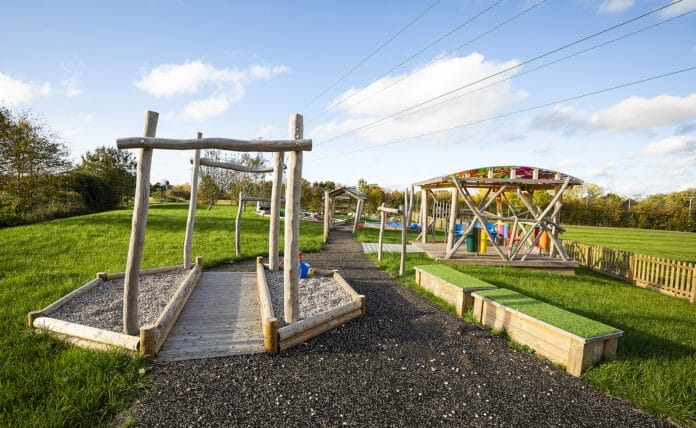
This project is a great example of how early stakeholder engagement and collaboration led to a successful delivery of the school on time and budget. Wokingham Borough Council approached the project with an open mind, keen to develop a modular approach. This was not a barrier to our creativity, in fact it helped create a safe and nurturing environment that inspires and gives a sense of place, helping future pupils achieve their full potential.
Michael Ruddick, Director at Reds10: “Constructing the school’s extension offsite meant that we were able to deliver the project more quickly, under safer, more controlled conditions and with less disruption to the local community. The Reds10 team are proud of the building we have delivered. While pushing the boundaries of off-site construction and providing a truly visually amazing educational space, we were able to significantly reduce the overall programme for delivery and achieve sustainable, enhanced carbon reduction features. All without compromising on the comfort of the building.”
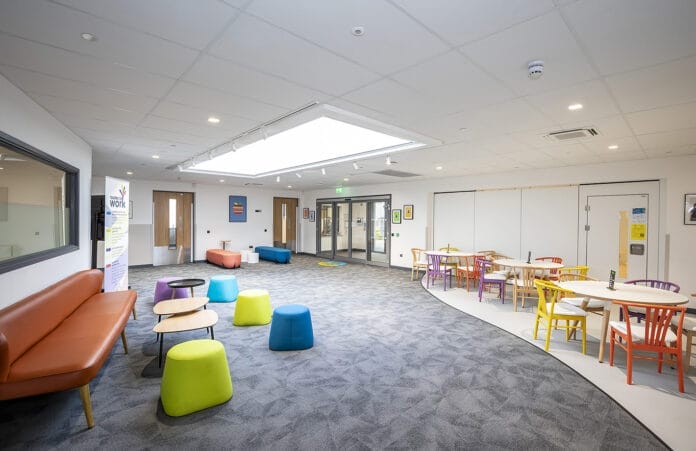
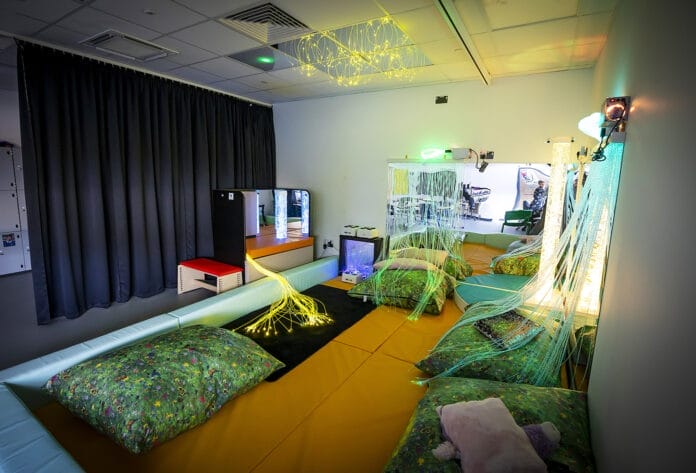